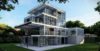
At beSteel, sustainability is more than just a priority: it is the very essence of our approach.
Less polluting and more efficient, our lightweight steel structures are designed to meet the challenges of modern construction. Discover how beSteel can transform your project into a sustainable and innovative achievement!
The construction industry in 3 key figures
Lightweight steel, the most effective and sustainable solution
to decarbonize the construction industry
Construction destroys natural habitats and reduces biodiversity through deforestation, soil artificialisation and the extraction of raw materials. Lightweight steel framing, a durable and recyclable material, offers an ideal solution to reduce carbon emissions and meet the EU’s target: -30% waste by 2030.
At beSteel, we combine lightweight steel and off-site manufacturing for clean, waste-free, and environmentally friendly construction sites. Discover why this innovative method outperforms traditional techniques and represents the future of sustainable construction.
Lightweight steel surpasses most other construction materials due to its exceptional combination of strength, weight, durability, and recyclability.
Lightweight steel: sustainable and innovative material
Thanks to its excellent strength-to-weight ratio, the amount of material required to build the same surface is significantly reduced.
For example, a standard house today is equivalent to approximately four car frames.
Moreover, steel’s ability to be reused and re-melted makes it an almost infinitely recyclable material. Not to mention the vast stock of steel already extracted on the planet, ready to be repurposed.
It is just waiting for one thing: to build the future.
-
1
Strength and efficiency
Lightweight steel offers an exceptional strength-to-weight ratio, ensuring the same structural integrity with fewer materials. This enhances the efficiency of construction projects while reducing overall resource consumption. -
2
Recyclability
With a recycling rate of 90%, steel is one of the most recyclable materials. Unlike treated wood, steel does not release carbon when burned, further enhancing its environmental benefits. -
3
Designed for Deconstruction
Our lightweight steel structures are designed to be easily disassembled, minimizing waste through a dry construction method. This approach promotes sustainability and reduces the total lifecycle cost of materials. -
4
Environmental Impact
Lightweight steel frameworks significantly reduce the carbon footprint of the construction industry. The adoption of these solutions could decrease carbon emissions by 44% by 2050, optimizing resource use and minimizing waste.
Off-site: a sustainable construction solution
Off-site manufacturing combines efficiency, waste reduction, and minimal environmental impact, making it an essential solution for more sustainable and responsible construction.
-
1
Waste Reduction
With precise planning and production in a controlled environment, off-site manufacturing minimizes errors and waste, both in the factory and on the construction site. Fewer unnecessary materials, less waste. -
2
Less transport, fewer emissions
Only the necessary, ready-to-use components are transported to the site, reducing vehicle trips and associated emissions. -
3
Faster construction
Off-site manufacturing speeds up timelines by 20 to 40%, minimizing disruptions to the environment and neighbors while optimizing efficiency. -
4
Reduced on-site labor
With 60% fewer personnel requirements, off-site construction provides less crowded and safer construction sites.
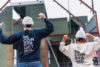
Need a Life Cycle Assessment (LCA) for your project?
If you need a Life Cycle Assessment (LCA) or an Environmental Product Declaration (EPD) for your steel framing project, our team is ready to provide you with all the necessary information.
Life Cycle Assessment (LCA):
the environmental impact of beSteel steelframe
In collaboration with Bouwen met Staal, the Dutch federation of steel frame builders, a comprehensive study has assessed the environmental impact of steel structures.
The analysis covered both heavy and light steel.
While this does not exactly correspond to beSteel structures, a dedicated study on light steel alone is not yet possible due to the novelty of this construction method in Europe.
Lightweight steel results:
- LCA: 1.39 kg CO₂ per 1 kg of steel or about 11.12 kg CO₂/m² of steel frame.
- ICE (Environmental Cost Indicator): 0.15 €/kg of steel over 100 years, or 1.17 €/m² of frame.
Comparison of environmental costs (ICE/m², according to the NMD database):
-
2.9
2.88 €/m2
Traditional masonry house
-
1.8
1.78 €/m2
Cross-laminated timber
-
0.6
0.61 €/m2
Untreated timber frames (in the Netherlands only).
With this data, we support your projects by providing tools to measure and reduce the carbon footprint using LCA software. Our commitment: lowering production costs and achieving carbon neutrality for our steel structures.
Reuse and Recycling of Steel Structures:
Light steel frame construction offers significant potential for material reuse and recycling at the end of its life cycle:
- Up to 80% of a building’s materials can be reused at the end of its life.
- Currently, as light steel framing is still a relatively new construction method, 25% of steel structures are reused without any loss of quality. However, the study adopts a cautious reference rate of 16% for reuse.
- At the end of its cycle, 95% of steel is recycled, limiting waste to just 5%.
Steel frame construction has great potential to reduce environmental impact while promoting material reuse and recycling.
Discover how we use this low-carbon steel in our projects in just 1 minute.
Our vision:
Carbon-neutral steel structures
At beSteel, we are committed to reducing the carbon footprint of our steel structures through the use of ArcelorMittal Magnelis® steel, combined with innovative xCarb™ initiatives:
xCarb™ Initiatives:
XCarb™ green steel certificates: Steel from ArcelorMittal’s decarbonization processes, proven to significantly reduce CO₂ emissions. Each purchase with this certificate supports carbon footprint reduction projects (production in Liège, Bremen, and Ghent for beSteel).
XCarb™ recycled and renewably produced: Steel produced in Spain using an electric furnace powered 100% by renewable energy. Made from 90% recycled materials.
Measured environmental impact:
Thanks to these innovations, the steel used in our structures allows for a reduction of CO₂ by up to 2110 kg per tonne, compared to the standard emission of 2570 kg of CO₂ per tonne of steel.
At beSteel, every structure contributes to a more sustainable future and carbon neutrality for the construction industry.
Watch the video above to learn more about xCarb™.
Cradle to Cradle Certified®:
A guarantee of sustainable commitment
The Cradle to Cradle Certified® program is a globally recognized standard that evaluates products based on several criteria to ensure their contribution to a healthy, fair, and sustainable future.
In 2019, beSteel was assessed and received the Bronze certification, highlighting our commitment to environmentally friendly practices.
How much CO₂ does beSteel help save?
Through our innovative solutions, beSteel actively contributes to reducing the environmental impact of construction. By combining data from our study and another conducted in Egypt (126.49 kg CO₂-eq/m²), we have calculated the total carbon savings achieved by our projects each year.
By 2031, beSteel will be able to avoid up to 60,000 tonnes of CO₂ in total!
