NEW STEEL FRAME
Anyone entering Ghent from the ring road, near the Einde Were French fry shop, can’t miss it: Wim Van Vynckt’s parquet floor has been enriched with two colorful new storeys. The lightweight steel-frame vertical extension, built by construction pioneer beSteel in collaboration with architect Maxime Balcaen and construction company KMK Construction, is the latest addition to the range.
beSteel re-launches #manybirdsfewnests campaign. The campaign focuses on demographic pressure, rapid urbanization and the need for densification. Lightweight steel with the off-site construction method makes vertical residential extension faster and more accessible.
Growing demographic pressures
With continued population growth, the housing shortage in Flanders and Belgium is rapidly increasing. According to the Federal Planning Bureau, Belgium’s population will increase by 1.3 million by 2070, bringing us to 12.9 million inhabitants. However, our cities are becoming increasingly crowded, and the space available for new housing is scarce. How do we solve this challenge?
‘This street art work makes the link between, on the one hand, the problems of hardening that shrink the natural habitat of many animals. On the other hand, the phrase #manybirdsfewnests (many birds, few nests) reminds us that the demand for housing exceeds the available supply. Many people are looking for a ‘nest’, preferably in a good location and of good quality. To solve the housing shortage and still keep our cities liveable, we will have to build vertically much more than we do today”: explains Hélène de Troostembergh, CEO of beSteel.
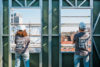
Steel frame vertical extension : the solution for urban density
1.Street Art Eyecatcher in Ghent
After its success in Antwerp in 2023, beSteel is turning its attention to Ghent this year. Together with architect Maxime Balcaen and construction company KMK Construction, beSteel added two new floors to Wim Van Vynckt’s parquet shop, located near the Ghent city ring road. This special design by graphic artist Davi Giolo makes the topping a real eye-catcher. Assembly began three weeks ago and was successfully completed last week. (October 2024)
2.Creating living space without extra land
The innovative technique of vertical extension – adding floors on top of existing buildings – offers a sustainable solution for cities struggling with population growth and limited building space. This concept is at the heart of beSteel’s #manybirdsfewnests campaign, which focuses on optimising urban space and aesthetics while limiting environmental impact.
With this elevation in Ghent, beSteel shows how urban expansion becomes possible without further land encroachment. This is the future-oriented solution that responds to the need for sustainable urban development and proves that we can offer creative, green answers to today’s major housing challenges.
‘One in five buildings in Paris has already been elevated throughout its history.’
Maxime Balcaen, architect and partner at platform architecture, on the history and future of the elevations:
‘Elevation is anything but new. As early as the Middle Ages, elevations were the norm in most European cities. Protective walls and ramparts restricted city expansion, while taxes were levied only on square metres of floor space, not the number of floors. For economic and security reasons, raising buildings was the solution to increase living space within the city. From the seventeenth century, new laws and reforms made it possible to add even more floors, until land ownership rules changed in the 1960s and the benefit of topping up diminished.’
In the past decade, the focus on elevation has increased again. The potential to raise buildings is enormous and should be systematically considered in renovation, redevelopment or extension projects. It allows us to make the best use of available space, while improving urban aesthetics and the quality of life of residents. Vertical extension offers an opportunity to densify our cities sustainably and thoughtfully, with an eye to both past and future.’
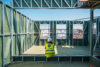
An innovative solution
beSteel is one of the pioneers of off-site construction, offering an innovative approach to the housing shortage. By producing steel structures in their factory, the entire floor is transported to the construction site in sections and installed in a matter of weeks. This method saves an enormous amount of time compared with traditional construction methods, and considerably reduces inconvenience for residents and neighbors.
-
-
- 1. Lightweight, fast, and sustainable : What makes beSteel’s steel frame solution unique is its light weight. The steel structure is up to 10 times lighter than traditional building materials and can be added onto existing buildings without placing excessive weight on the structure. This flexible and sustainable steel extension system is also easy to dismantle and fully recyclable—essential qualities at a time when sustainability and circularity are increasingly important.
- 2. A greener construction sector : With over 30% of global CO₂ emissions coming from the construction sector, the need for environmentally friendly solutions is urgent. beSteel addresses this by using lighter, offsite-produced steel frame constructions, which significantly reduce the ecological footprint. Steel can be reused and recycled almost infinitely, reducing CO₂ emissions by nearly 50% compared to traditional concrete construction.
-
-
5 benefits of the beSteel system
- Lightweight: The lightest construction system on the market, ideal for extensions without the need for additional structural reinforcement.
- Efficiency: The structure can be quickly assembled, allowing for strict adherence to scheduling and minimizing disruption.
- Sustainable and circular: Offsite production reduces waste and requires less manpower, resulting in a lower ecological footprint.
- Recycling and reuse: Steel can be recycled almost indefinitely, offering a sustainable, future-proof solution.
- Local production and control: All steel frames are produced in BuildUp’s Aarschot factory, ensuring close project monitoring and high quality.